What is Porosity in Welding: Typical Sources and Efficient Remedies
What is Porosity in Welding: Typical Sources and Efficient Remedies
Blog Article
Recognizing Porosity in Welding: Exploring Causes, Results, and Avoidance Strategies
Porosity in welding is a relentless obstacle that can dramatically influence the quality and stability of welds. As professionals in the welding industry are well mindful, comprehending the causes, results, and avoidance techniques connected to porosity is essential for attaining durable and reliable welds. By delving into the origin of porosity, examining its detrimental results on weld top quality, and exploring efficient avoidance strategies, welders can improve their understanding and abilities to produce high-quality welds continually. The detailed interplay of factors contributing to porosity calls for a detailed understanding and an aggressive technique to make certain successful welding end results.
Typical Reasons For Porosity
Contamination, in the type of dirt, oil, or corrosion on the welding surface, produces gas pockets when warmed, leading to porosity in the weld. Inappropriate protecting happens when the securing gas, generally made use of in processes like MIG and TIG welding, is incapable to fully protect the molten weld pool from responding with the bordering air, resulting in gas entrapment and subsequent porosity. Furthermore, inadequate gas protection, usually due to wrong circulation rates or nozzle positioning, can leave components of the weld unprotected, permitting porosity to form.
Impacts on Weld Top Quality
The existence of porosity in a weld can dramatically jeopardize the general top quality and stability of the bonded joint. Porosity within a weld develops spaces or dental caries that damage the framework, making it much more at risk to cracking, corrosion, and mechanical failing.
In addition, porosity can impede the performance of non-destructive screening (NDT) strategies, making it challenging to spot other issues or stoppages within the weld. This can cause considerable security worries, specifically in important applications where the structural integrity of the bonded elements is paramount.
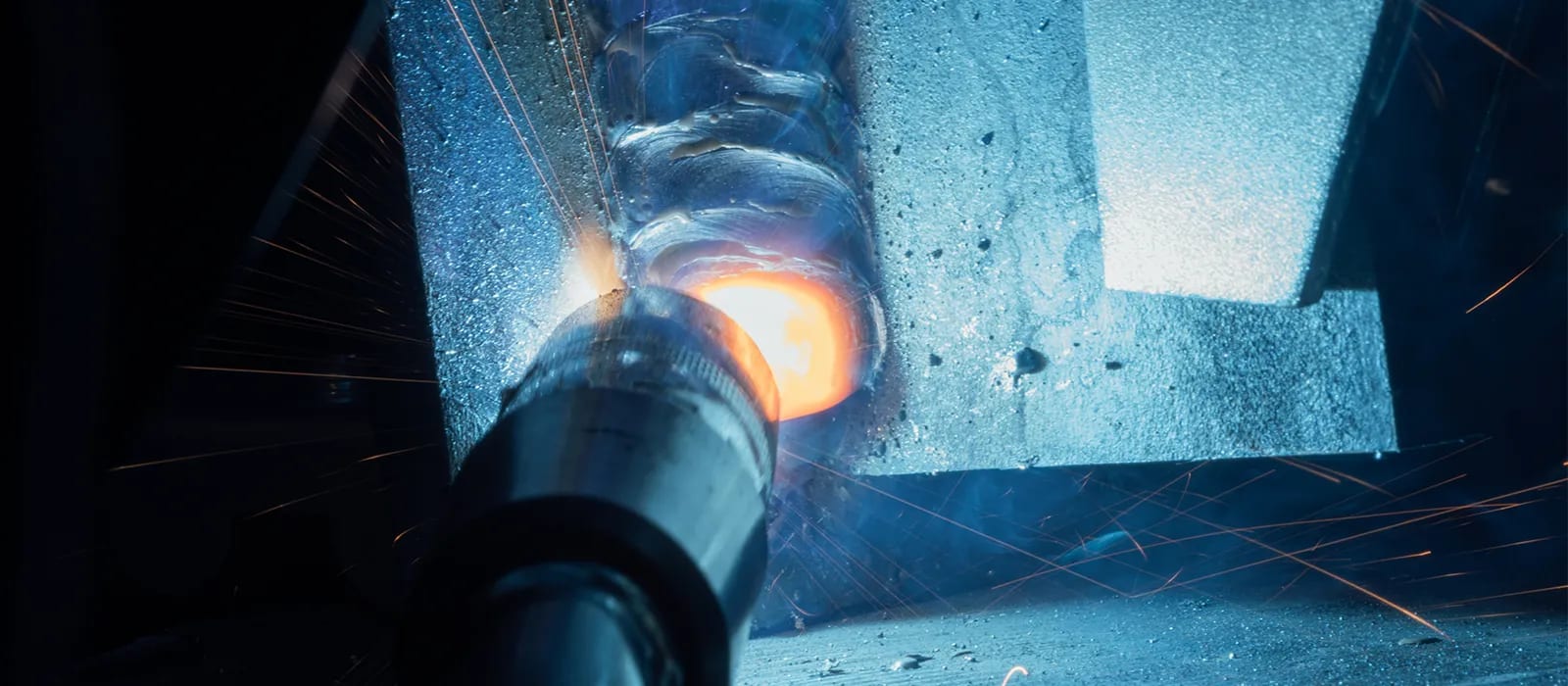
Avoidance Techniques Review
Offered the damaging impact of porosity on weld high quality, efficient prevention strategies are vital to preserving the architectural honesty of welded joints. Among the main avoidance methods is comprehensive cleaning of the base materials prior to welding. Pollutants such as oil, grease, corrosion, and wetness can add to porosity, so making sure a tidy work surface area is necessary. Appropriate storage of welding consumables in dry conditions is also vital to stop dampness absorption, which can cause gas entrapment throughout welding. In addition, choosing the ideal welding parameters, such as voltage, current, and travel rate, can assist decrease the risk of porosity formation. Guaranteeing visit this site appropriate securing gas circulation and coverage is another critical prevention technique, as inadequate gas insurance coverage can lead to climatic contamination and porosity. Proper welder training and qualification are necessary for executing preventative procedures successfully and constantly. By incorporating these prevention techniques right into welding techniques, the occurrence of porosity can be dramatically minimized, leading to stronger and more reliable bonded joints.
Significance of Proper Shielding
Appropriate shielding in welding plays an important duty in avoiding atmospheric contamination and making sure the integrity of bonded joints. Protecting gases, such as argon, helium, or a blend of both, are commonly utilized to safeguard the weld pool from responding with aspects in the air like oxygen and nitrogen. When these reactive components enter call with the hot weld swimming pool, they can trigger porosity, bring about weak welds with reduced mechanical residential properties.
Inadequate shielding can result in numerous problems like porosity, spatter, and oxidation, compromising the structural integrity of the welded joint. Adhering to proper shielding techniques is necessary to produce high-grade welds with marginal flaws and ensure the long life and dependability of the welded parts.
Monitoring and Control Approaches
How can welders effectively check and control the welding procedure to ensure optimum results and avoid flaws like porosity? By continually checking these variables, welders can recognize inconsistencies from the excellent conditions and make instant modifications to prevent porosity development.

In addition, applying appropriate training programs for welders is vital for monitoring and regulating the welding process effectively. What helpful hints is Porosity. look at here now Informing welders on the relevance of preserving constant specifications, such as appropriate gas shielding and travel speed, can assist prevent porosity concerns. Normal evaluations and qualifications can additionally make sure that welders excel in tracking and regulating welding processes
In addition, using automated welding systems can improve surveillance and control abilities. These systems can precisely manage welding parameters, reducing the chance of human mistake and ensuring regular weld top quality. By combining sophisticated tracking innovations, training programs, and automated systems, welders can properly check and regulate the welding process to reduce porosity problems and achieve top quality welds.
Conclusion
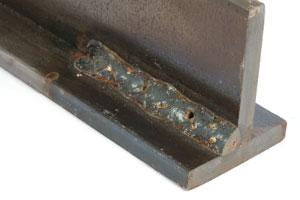
Report this page